Mr. Satoshi Ezawa, Director and COO of Scene, Inc.
Manufacturing sites require meticulous manual assembly work, and the complexity of documenting procedures and instructions, as well as communicating that information, is one of the core causes of low productivity. Scene Inc. has developed a 3D documentation tool called “Scene” that enables the efficient communication of product information using 3D CAD data even in situations where workers are not good at IT or where there are no high-spec PCs. We interviewed Mr. Satoshi Ezawa, the Director and COO of the company, about digital transformation (DX) in the manufacturing industry.
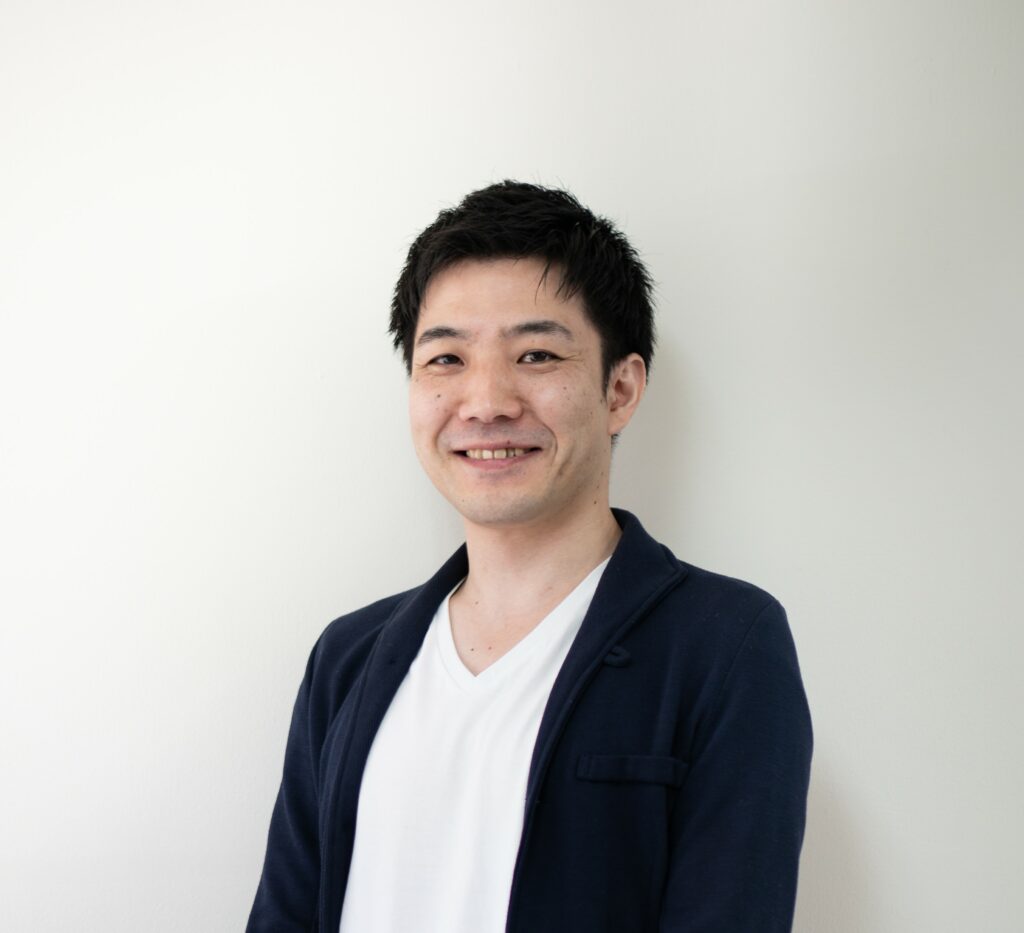
―First, what is the current state of the manufacturing industry?
The industry is increasingly adapting to the market needs for high-mix low-volume production and shorter delivery times. Such products still cannot be mass-produced by machines, so technicians have to manually assemble them. Meanwhile, overseas manufacturing quality and productivity are rapidly improving, and Japan’s strengths that have been traditionally achieved through human resources may no longer remain effective. To respond to this situation, it is now vital to reform the engineering chain, which is a series of business processes from product planning and R&D to product design, process design, and manufacturing.
―Does your tool enable manufacturers to reform the engineering chain?
Yes, it does. We are working on the digitalization of assembly procedures and other materials as well as information transmission through the secondary use of 3D-CAD design data. We are making digital technology into a tool that everyone can use to help engineers concentrate on their work with higher added value and demonstrate their full abilities.
―What tool do you offer?
We offer a documentation tool that makes it extremely easy for anyone to document easy-to-understand assembly procedures and instructions that explain the processes with 3D animations. Three-dimensional drawings based on 3D-CAD data have become popular in the design field, but they haven’t been successfully utilized in the later stages.
For example, Yamato Scientific Co., Ltd., one of our customers, used to communicate information between designers and assembly workers over drawings. They took pictures of the machinery and pasted them into Excel or pasted CAD data screenshots into PowerPoint to illustrate procedures and other materials. Preparing physical machinery and editing that data took a lot of time and effort, and even then it was hard to convey intent. The company then adopted Scene, which has since successfully solved every one of those problems.
―Please tell us more about how you use 3D-CAD data.
The user loads 3D-CAD design data into the documentation tool Scene and adds as many pages as they want while inserting objects, such as text boxes, arrows, squares, and images, to create a slide presentation with automated animations. You can basically imagine it as a tool that combines 3D technology with general presentation software.
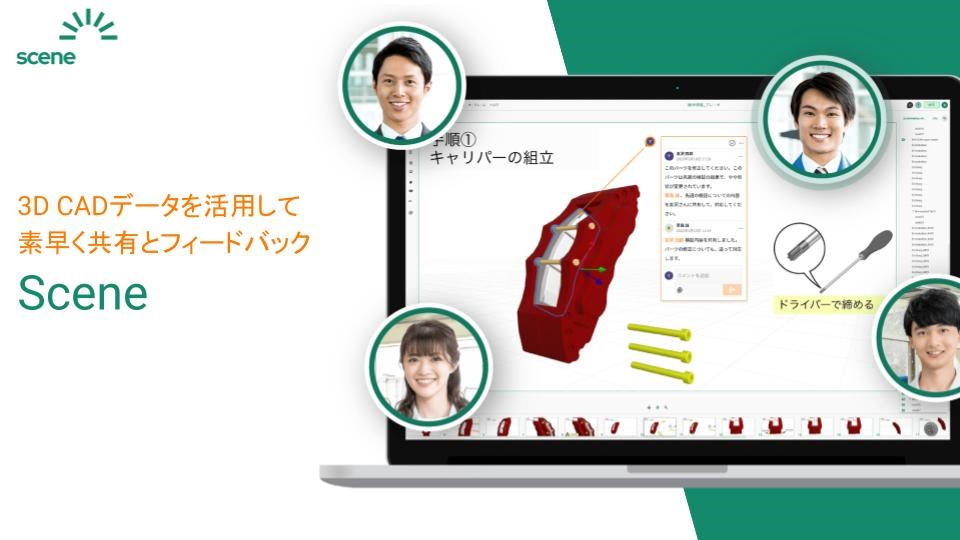
―It seems like your tool makes it possible to create an extremely clear procedure manual.
Moreover, it’s a browser-based tool, so the people involved can share it across departments to discuss. Its comment function also enables communication with people in remote places like foreign countries. While there are other tools, such as Google Slides, that enable communication over documents, they have never been able to capture 3D data.
―It’s very efficient to be able to share details digitally without having to prepare the actual equipment.
That’s right. We can digitize manufacturing and create a system for efficient work. Recently, “front-loading” has become a buzzword in the manufacturing industry. It refers to improving quality by investing resources in the initial processes to take measures against possible problems in the later processes . For example, creating highly accurate blueprints as early as possible to prevent design changes in the later processes leads to improvement in productivity. To achieve this, it’s important to absorb and organize information from every department through communication at the design stage.
―That means Scene naturally leads to front-loading. By the way, 3D-CAD data can be classified information. What security do you provide?
3D visual data is different from the original CAD data, so original data can’t be extracted from it. However, some companies have policies that prohibit the use of cloud data software and storage. In that case, we offer an on-premise (ie., owned by the company for internal use) version.
―It seems that the progress of digitalization in the manufacturing industry varies from company to company. How has the response to Scene been?
Recently, we have been exhibiting at numerous trade shows and have received a lot of positive feedback from companies that deal with high-mix low-volume and tailored products, such as analytical equipment, sensors, heavy industrial products, and industrial equipment. We are also working to eliminate paper-based work records by integrating 3D documents and work check sheets into our service. We believe that our tool will expand the possibilities of DX beyond simplifying the preparation of procedures and improving communication efficiency. It hasn’t been linked with existing platforms yet, but in the future, we hope to develop it into a tool that allows users to input and share anything with everyone involved.
―Is the tool only available in Japan?
We are currently focusing on the domestic market, but have a French customer who manufactures electric carriers, partly because we launched a global advertising campaign in our early stages of development. We’d like to expand overseas once our sales increase and become more stable in Japan.
Actually, we’d also like to use our Scene business to address global poverty and disparities. Our documentation tool also has applications in skills transferring and engineer training, so it has the potential to contribute to the economic development of developing countries. We’ve already been offered an investment by an international financial institution.
―That’s amazing. By the way, why did you start this business?
I studied liberal arts in college, but after graduation, I worked as a sales representative at Nitto Denko Corporation, a chemical manufacturer, for about three years, and then engaged in projects like operational reforms and supply chain management for the manufacturing industry at the consulting company EY Advisory and Consulting Co., Ltd. (currently EY Strategy and Consulting Co., Ltd). After that, I joined Accenture, where I gradually developed the desire to start my own business. So, I moved to a space-related startup called Infostella and worked as a business planner. Infostella is a company that builds antenna networks for small satellites. I then co-founded Scene with Vijayan Swathinath, one of my colleagues at Infostella.
―What are your future prospects?
3D-CAD data captured by our documentation tool is entirely the product information of the customer and is at the core of manufacturing. Placing this data that’s usually only found in production flow charts and bills of materials at the very core, we plan to develop our tool into an information management system for product lifecycle management (PLM). Existing PLM tools aren’t very customizable or flexible, and it usually takes years to implement them as system-wide infrastructure. They also often require burdensome customizations, which is a costly challenge for customers. Therefore, our long-term vision is to develop Scene into a headless (*) and highly customizable PLM tool.
In addition, we are pioneering the application of our technology to projects not for companies’ internal use but for their customers, such as service manuals and marketing materials. We hope to cover these projects step by step in the future.
*Headless: System architecture that separates the front end from the back end to improve the quality of the user interface and the efficiency of maintenance and operation
Company name:Scene Inc. |
Founded:December 2019 |
Number of employees:4 |
Main business:Planning, developing, operating, and selling the 3D documentation tool Scene URL:https://www.scene.space/en |
This article is part of a series of articles introducing venture companies working together as ICF members to resolve societal issues.