Mr. Minoru Ike, Representative Director of Tokyo Factory, Inc.
Manufacturing processes in heavy industry and other industries involve many components, people, and steps. There are often barriers within these processes that restrict businesses’ ability to things like share manufacturing information and hand down techniques. Focusing on these issues, Tokyo Factory, Inc. is working on visualizing manufacturing information throughout supply chains and building manufacturing information databases. We interviewed Mr. Minoru Ike, the Representative Director of the company.
―Please tell us about Tokyo Factory, Inc.
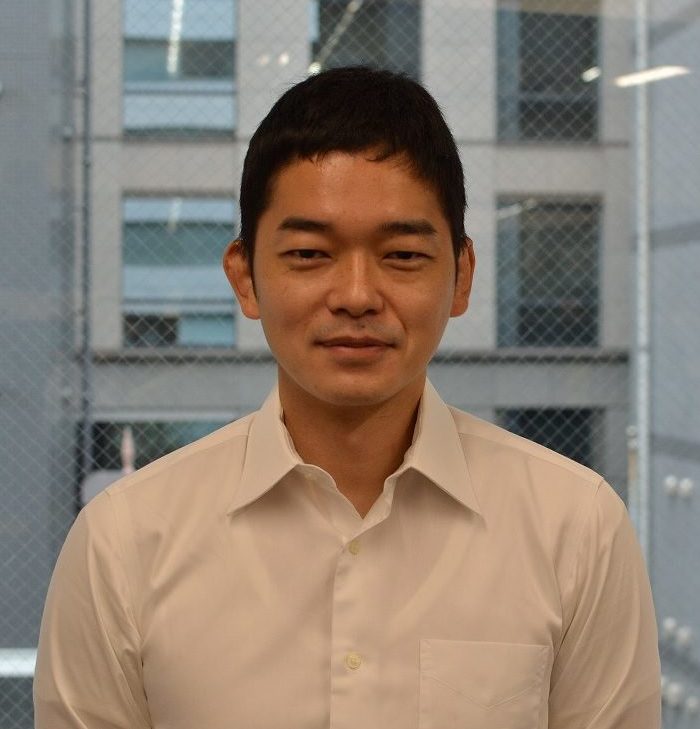
Representative Director of Tokyo Factory, Inc.
We are an early-stage startup founded in 2020 with about 25 employees. We provide the Proceed Cloud, which is basically a SaaS specialized for manufacturing sites.
―Why did you decide to develop a service specialized for manufacturing sites?
I have been involved in the manufacturing industry for a long time, and I always felt that production sites in heavy industry were far behind in digitization.
At so many sites, operations had not changed in half a century; I’ve even seen paper drawings and on-site blackboards and whiteboards still in use.
I also felt that information on production sites was inefficiently dispersed. Since information could be found in multiple places, such as systems for counting work hours, daily reports, on-site bulletin boards, e-mails, and local computer folders, it was difficult to conduct reviews and audits for improvement. The lack of information sharing was also preventing the visualization of supply chains. Thus, this was another issue to be addressed.
―Please tell us about the specifics of your product.
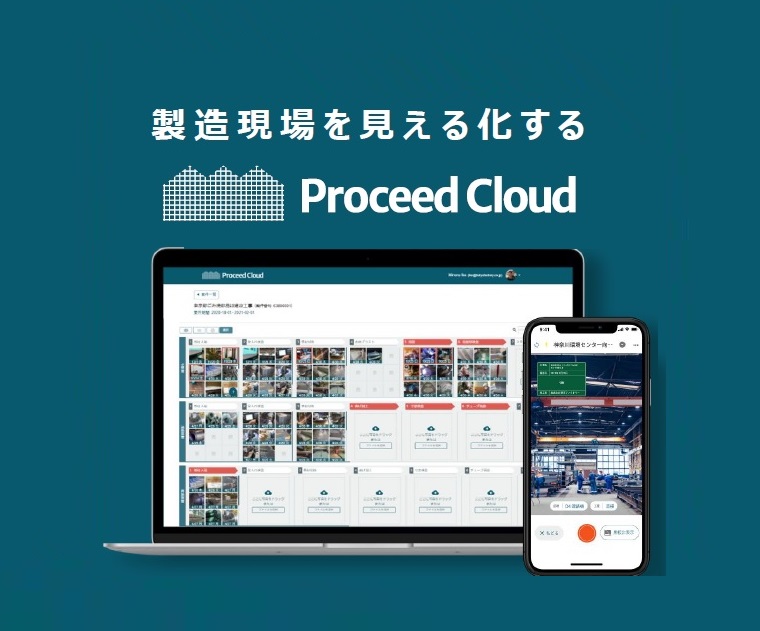
We offer a digital tool for manufacturers called the Proceed Cloud.
The Proceed Cloud builds manufacturing information databases based on photos and can visualize supply chains.
In the case of a large structure, some defects are often found at the time of delivery. If this occurs, the manufacturer must prove that there are no problems with the manufacturing processes. Therefore, manufacturers keep records by taking dozens of photos of their manufacturing processes every day.
Since they usually store these photos locally on computers, there is a lag between the taking and storing of the photos, so they may become unsure of what the photos are about. Or, the structure of the folders may become too complex, which makes it difficult to tell which photos are in which folder. This kind of thing has been happening on a daily basis.
The Proceed Cloud lets users map and store photos on two axes: vertical and horizontal. For example, if you set the two axes to “component” and “process,” you can easily see which component in which process is in the stored photos.
In this way, the Proceed Cloud can greatly reduce the time and effort required to search for photos.
―After taking photos, should users put them in the Proceed Cloud?
Photos taken with a digital camera can be uploaded to the cloud by dragging and dropping them on the computer where they are stored, and a new view permission is shared.
Recently, there are more and more people taking photos with smartphones, so we also provide a mobile app. The app has a button that allows the user to start the camera.
When the camera starts, two buttons will appear that allow the user to select items for the vertical and horizontal axes. When the user takes a photo after selection, the photo is automatically uploaded to the folder defined by the two axes.
This enables those who cannot go to the production site every day to grasp what is happening on-site in near real time. These people include, for example, managers of products outsourced overseas, line managers in the manufacturing department, and designers.
―In addition to photo management, are there any other issues that Proceed Cloud can resolve?
Production processes in heavy industry often take six months, one year, or more. As a result, it takes a very long time to train young people.
The Proceed Cloud allows users to take photos of a series of processes, from receiving components to shipping finished products. This means that they can have some understanding of what their manufacturing processes look like without having to go to the production site and see it in real time over many months.
―Can users add comments or other information to photos stored in the Proceed Cloud?
Yes, they can add comments and tags. This function enables them to increase the usability of their databases.
For example, on a photo taken by an inexperienced person, an experienced person might comment, “Please remove the weld line because it looks bad.” Comments like this would have been conveyed verbally in the field. These are minute but important distinctions that are not written in standard procedures or guidelines. The cloud can accumulate this kind of tacit knowledge.
In terms of tagging, labeling photos with words such as “defect” or “weld crack” enables search across many projects at once. Users can also narrow their search by photographer, date, and/or information in comments.
In addition, users can also post and comment from the mobile app, so if they notice something in the field, they can quickly post it and send a message.
―What are the advantages of using the Proceed Cloud?
One of the advantages is that on-site work becomes easier.
In the past, photos taken with digital cameras have been organized and stored where they tend to accumulate to some extent. It would be good if they could be shared, but there are few opportunities to see other people’s photos because local computer folders or privately shared servers are usually used.
To solve this problem, the Proceed Cloud allows users to organize and share photos at the time and place of shooting. Users can share new information quickly with much higher work efficiency. They can also then communicate based on the photos.
There are also medium- and long-term advantages.
The more the Proceed Cloud is used, the more it builds up the database of production information. This in turn will streamline the transmission of technology.
―How many companies have adopted the cloud?
The Proceed Cloud was fully launched in September 2021. At present, approximately 30 companies in eight countries have adopted it.
We hope that more companies will adopt it in the future to improve operational efficiency and technical skill transfer capacity.
Company name:Tokyo Factory, Inc. |
Founded:April 2020 |
Number of employees:4 (25 including outsourcees) |
Main businesses:Development, sales, and operation of manufacturing SaaS and consulting for business improvement URL:https://tokyofactory.co.jp |
This article is part of a series of articles introducing venture companies working together as ICF members to resolve societal issues.